Will the Real Lean Production Please Stand Up?
The Internet can make for some truly random points of contact. Under normal circumstances rabble-rousing labor journalists/activists rarely inhabit the same room as management efficiency gurus--let alone exchange words.
Yet, when members of the “lean community” (their actual phrase) took issue with my recent claim that big hotel chains' embrace of lean management techniques are a contributing trend to high injury rates for housekeepers, it's hard not to say the debate is on, brothers and sisters.
To be fair, the leanies talk like a decidedly high-road crowd when it comes to concern for workers—at least for my low bar for management theorists. They (rightly) put scorn on the hotels for crudely speeding up work and hurting workers in the process. They are quick to heap abuse on a supposed misapplication of lean production techniques for being LAME (Lean as Misguidedly Executed). They even point to a single case of a Canadian nurses' union embracing lean.
But they are just as quick to play the “LAME” game with Labor Notes' understanding of lean production. At this point, most longtime readers would likely have the same colorful reaction as my friend (and co-author of a pamphlet condemning lean production from a workers' perspective): “My response involves making certain hand and arm gestures which are unreproducible on e-mail.”
Nevertheless, it’s worthwhile to revisit what lean production is and isn't.
I concede to the leanies that lean—in its self-conception—is first about reducing “waste.” Modeled after Toyota's famed manufacturing techniques, one of its central features is kaizen, a constant process of improvement. In theory, a more efficiently-organized workplace would be a safer, happier workplace.
If lean was simply about this, who wouldn't be for it?
A WHOLE OTHER LAME
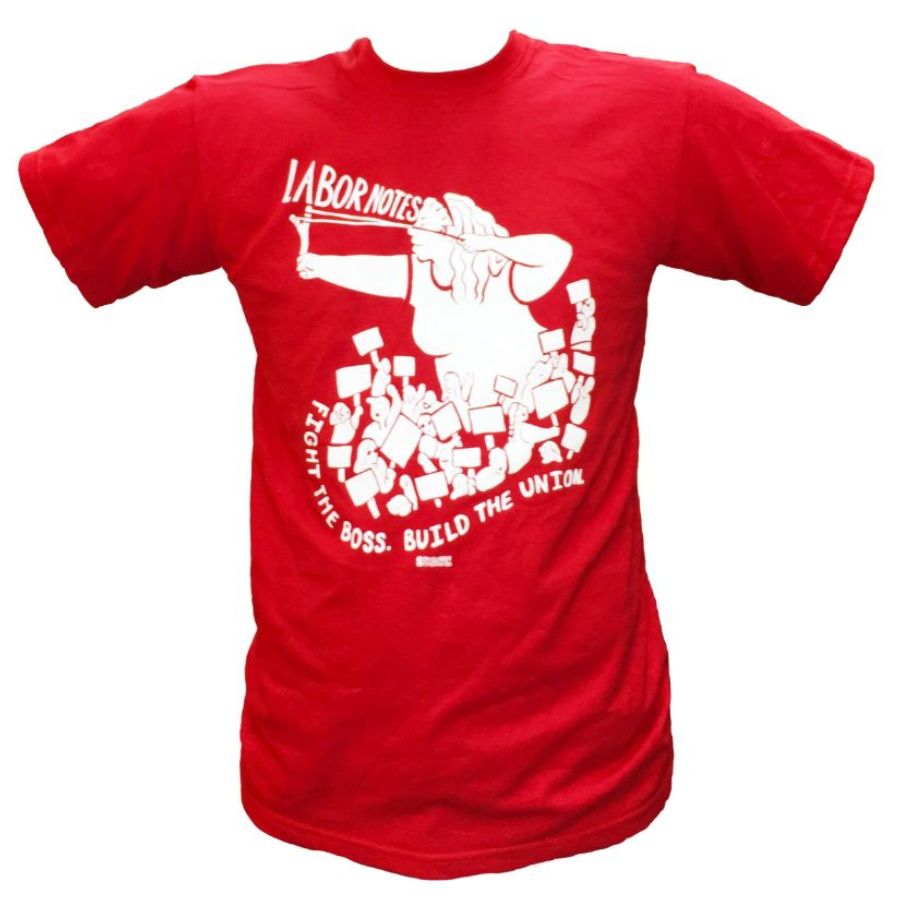
SUPPORT LABOR NOTES
BECOME A MONTHLY DONOR
Give $10 a month or more and get our "Fight the Boss, Build the Union" T-shirt.
For nearly two decades, though, Labor Notes has reported, analyzed , and organized against lean as it has been experienced on the ground in North America. Tens of thousands of workers who’ve been on a lean line have found a whole other LAME: Lean as Mainly Experienced. It has frequently meant fewer workers doing more work in jobs they control less and less.
For them, lean has meant “management by stress,” that is, a constant fine-tuning of work that often leads to a stressful and disempowering environment on the shop floor. Despite claims of harnessing the creativity of workers, it has also meant de-skilling as managers introduce a range of activities to undermine the skill sets that workers develop on the job. Instead workers are placed before an ever-proliferating set of more mindless tasks. It has often meant creating “flexible” shifts and work to suit this finely-tuned system, which often means turning full-time steady work into part-time or temporary work—and on occasion dispensing with it altogether through subcontracting.
While these processes have undercut workers’ control over their jobs, they have also undercut hard-fought work rules in unionized contracts and, in the case of the various team management schemes, the union itself.
More dramatically, in many lean places the case can be made that workers are injured at a faster pace than in more traditionally-organized workplaces. And it hasn't just been unions criticizing it: a number of serious studies have backed this counter-view. One sweeping study in the Journal of Occupational Health Psychology compiled the results of a number of studies conducted in the 1990s when these schemes were hottest.
And one can look back to a more contemporary example in the lean flagship, Toyota. At one of its key U.S. manufacturing facilities, in Georgetown, Kentucky, the New York Times reported in 2007 over 1,800 cases of workers injured who never returned to work on the line.
This is the kind of lean production that we as a movement could and should be continuing the fight against. As the headline of a capstone piece in a Labor Notes series on work reorganization schemes put it: surrendering the shop floor means surrendering the future. And in that fight there can be no surrender.