Slow Walks and Tough Talk: Auto Workers Turn the Screws
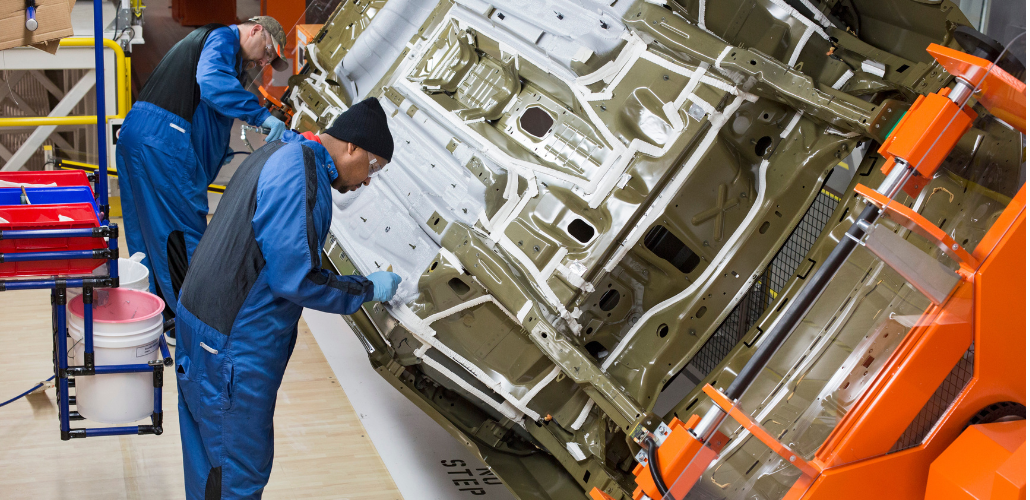
This pre-strike photo shows workers in the paint shop at Sterling Heights Assembly Plant, one of many Big 3 plants that have not yet been called out on the UAW's gradually escalating Stand-Up Strike. In many plants, auto workers still on the job are finding creative ways to slow production to a crawl. Photo: Jim West/jimwestphoto.com
The 18,000 Auto Workers on strike have lit up the labor movement. But the strike is only the most visible side of auto workers’ leverage.
The less visible side is on the shop floor, where organized refusals of voluntary overtime have shut down multiple lines and whole factories for entire weekends since the strike began.
Among the 130,000 UAW members still working at the Big 3 auto companies, shop floor creativity is bringing back a bold tradition of “work to rule”—where workers coordinate to do only their explicit duties by the book, and nothing more. When production slows to a crawl, it proves how workers’ savvy was what kept the factory humming to begin with.
The reform caucus Unite All Workers for Democracy, which backed the election of President Shawn Fain and the rest of his Members United slate, has become a hub for these militant tactics. UAWD’s weekly “Members’ Update” calls and a “Members’ Voice” strike bulletin focus on spreading tactics to push managers and bring more co-workers into action.
The caucus launched a Refuse Voluntary Overtime pledge; members have used the pledge and its leaflets to rapidly organize hundreds of co-workers to join the refusal.
The rebellion from the ranks is forcing management to scramble for a counterattack. In the last week, hoping to keep those profitable Escalades and F-150s rolling out, managers at plants across the Big 3 tried to make weekend overtime mandatory.
But members at many plants figured out new ways to hold the line with their striking siblings. Some are declining to take the usual shortcuts, like riding bicycles around a big plant. Others are exploiting the unique legal environment of working under an expired contract: it is now an unfair labor practice for management to make unilateral changes to wages or working conditions. If bosses want to change something, they have to bargain it.
Auto Workers at four plants shared these dispatches on their co-workers’ latest inventions.
NO TORQUE INSPECTOR, NO TRUCKS
Eric Truss, Ford Rouge Complex, Michigan:
“After Shawn requested that people refuse voluntary overtime, the company asked us to sign up for Sunday overtime. There’s two lines in my department. I asked everybody to refuse it. We just talk to each other while we’re working on the line, sometimes on break.
“There are two-tiers [newer hires at lower pay and benefits] who wanted to work the OT, but I pulled them aside and said, ‘You know there are tier-twos out on strike just like you, who don’t have this opportunity for any work at all. If we do our part, we won't leave them stranded.’ I think that helped to show them we could have their back. My line agreed to refuse the overtime.
“The other line in my department has a lot of tier-twos. I talked to them, and eventually they mostly agreed. The plant needed 11 people to run that line, but only got eight.
“The next thing we knew, we heard some people changed their mind and actually wanted to do work. This is when a torque inspector for that line approached me. She said, ‘I don’t want to do OT, I want to support the picket line. I'm going to speak to others.’
“Torque inspectors make sure bolts and nuts are tightened to the required spec. These are line workers, a classified job they’d have to sign up for and get trained for. They each have multiple backups, who are at a lower tier.
“After she talked to them, they all refused. That shut down the whole line.
“Management knew that without those torque inspectors, they had to shut it down. Those are government-required parts. They have to be inspected.
“That particular line feeds the assembly plant for the electric F-150. Without that one line running, it could put the EV plant at a critical low on its supply chain. Which is amazing because it’s torque checkers on a small line of 12 people who could possibly shut down the whole EV plant.”
STAYING OFF THE BIKE
Tiffany Martin, General Motors Arlington Assembly, Texas:
“Now even the electricians are refusing the overtime. And I noticed a few of them not using their bicycles to get to the breakdowns in the line. They have been walking without any rush.”
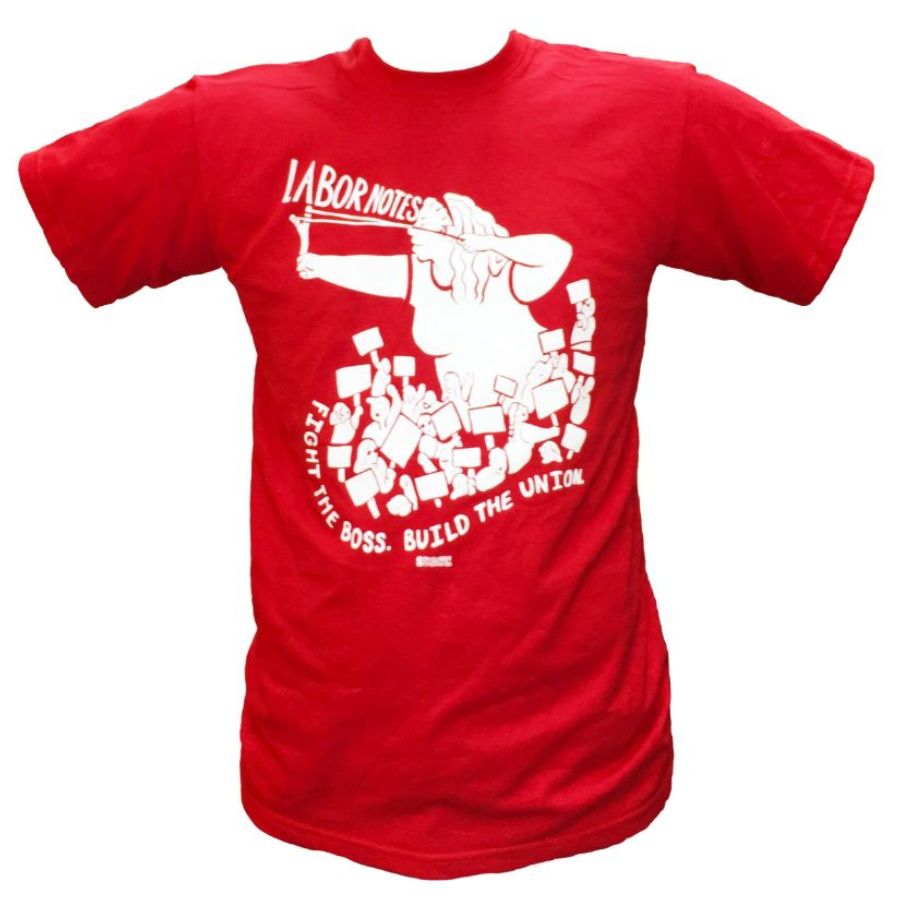
SUPPORT LABOR NOTES
BECOME A MONTHLY DONOR
Give $10 a month or more and get our "Fight the Boss, Build the Union" T-shirt.
[GM Arlington covers 250 acres, with more than 5,000 workers on site. Like at many other huge plants, UAW electricians and tradespeople who repair breakdowns typically use bikes to move quickly across the floor. But nothing in their job description explicitly requires going on wheels. Walking, especially carrying toolbags, might take an extra 15 minutes between each broken station stopping the line.]
MANDATORY O.T.? THAT’S A UNILATERAL CHANGE
Luigi Gjokaj, Local 51 vice president, Stellantis Mack Assembly Plant, Michigan:
“Before the contract expired, we’ve been running mandatory shifts on two out of every three Saturdays.
“Two weekends back, plant managers sent out a message canceling Saturday shifts. Then a manager sent out a message uncancelling that, calling us back in after the Thursday deadline to announce a mandatory Saturday shift. They wanted to call back in all the TPTs [temporary part-time workers]. But then the message got sent to many full-timers too.
“Our stewards heard about that right away. We considered that a unilateral change out of contract. We went right to the complex manager. He agreed to send a correction, and not give anybody hits for not doing the shift.
“For last Saturday, management decided to mandate all the TPTs to come in, because they couldn’t get enough people to sign up voluntary.
“But that meant calling in third-shift TPTs who worked Thursday into Friday night, getting to bed at 8 on Friday morning, who now had to figure out how to come in Saturday at 6 in the morning. Your normal sleep schedule and family schedule is thrown into craziness. I’ve never seen that in 13 years in the company.
“Me and the president went in and raised hell with managers. He’s usually a pretty calm guy with management, but he said, ‘I’m telling people not to come in. You can fire me if you want.’ Management sobered up fast. We got a verbal agreement: you can ask people, but not mandate the overtime.
“Then a few hours later, robocalls went out to all our TPTs saying you have to come in. Management reneged on our agreement. Maybe by mistake, but who knows. I wanted to file labor charges right away; I was raring to go. We decided to keep a bad-faith bargaining charge in our back pocket, but slap them with an RFI [Request for Information] to get all the dirt we could.
“The mandatory shift was a debacle. Half of the people didn’t show up. It was so bad they couldn’t run a single vehicle on production.
“I had to keep reminding them: you do not have the management rights clause anymore. We are in an expired contract—it’s different rules to the game! Typically, we have schedules and shifts, you’ve got to give us 14 days’ notice. But now every change you’ve got to bargain with us first.
“We’re hawking every little change they're making, like job assignments or parts moves. Anything out of the ordinary, we’re pushing back. We’re paying attention to discipline; are they giving a written warning or time off when they would have done a verbal warning before? Our stewards are on high alert. Our committee people are being very diligent.
“Management has been real quiet this week. They’re a little gun-shy now.”
MAKING THEM EARN IT
Ryder Littlejohn, Ford Buffalo Stamping, New York:
“Management is now making Saturdays mandatory. A lot of our skilled trades that run the lines have not been showing up, using sick days, FMLA [Family and Medical Leave Act] days, or just not coming and taking the AWOL [absence without leave] or write-up. So they can’t run the lines anyway.
“Also, they tried to use the people from the press side of the plant on the metal side because they could not run presses. Press side is where they stamp steel or aluminum into parts like hoods or door panels. Then they get sent to the metal side to be assembled into usable parts and sent to the assembly plant.
“Managers tried to move people based on their presses being down, because trades didn’t show up to run them. That’s a violation of the agreement.
“They all started to protest being sent over there. They all reported it to their committeeperson [union rep]. The fact that their work schedule was changed could be an unfair labor practice charge.
“Chances are in the end they would have had to go over, but the company gave up. It’s what we call ‘making them earn it.’”