The Persistent Problem of Health and Safety in the Auto Industry
Whether assembling cars, stamping out auto bodies, or making parts, an auto plant is one of the most dangerous places to work in the United States. While the number of fatalities in the private sector dropped somewhat from 1993 through 1998, they rose 50 percent in the auto industry over the same period. This was before the disastrous 1999 explosion at the Ford Rouge complex near Detroit that killed six.
In terms of non-fatal injuries and illnesses, auto assembly and stamping facilities consistently make the Bureau of Labor Statistics' 25 most dangerous list. Parts plants are not far behind. The rate for the industry as a whole ran almost three times that for the private economy in 1998.
Yet the official figures, compiled by the Bureau of Labor Statistics, show a decline in auto industry injuries and illnesses from 1994 through 1998--from 239,000 in 1994 to 182,000 in 1998, the last year for which there are figures. This significant drop runs counter to the traditional pattern in which periods of economic growth and high production, not to mention rising overtime, typically produce more accidents, stress, and disease.
The official explanation for this unusual decline in auto, as for a similar decline in the economy as a whole, is that employers began to take health and safety more seriously as the costs of workers compensation and insurance soared from the mid-1980s to the early 1990s.
MAXIMIZING PRODUCTION
A look at recorded OSHA violations at major auto companies, however, casts doubt on this explanation. DaimlerChrysler, General Motors, and Ford all showed a rise in the average number of detected violations from the mid-1990s through the first half of 2000. Ford broke some kind of record with a massive total of 344 OSHA violations from 1998 through July 2000, not including those associated with the Rouge plant explosion.
It can be argued that the discovery and, presumably, the correction of all these violations headed off real injuries or illness, thus contributing to an eventual decrease in actual incidents--at least after 1998. What cannot be argued is that they show increased concern by the corporations for the safety or health of their employees.
What is most likely is that the dramatic jump in OSHA violations resulted from management's obsession with maximizing production in the superheated economy of the late 1990s at a time when the companies were also trying to reduce their workforce.
In its 1999 Annual Report, for example, GM not only brags about its fast rising sales and exploding profits, but also about how it cut the number of its "excess workers" in half and its total North American workforce by 6,000 (in addition to the 14,000 person Delphi spin-off) from 1997 through 1999.
Equally dramatic was the increase in overtime, which jumped by 4.4 hours from 1991 to 1998 to an average of over seven hours per week.
As Business Week recently noted, break-neck production and swelling overtime appear to have had an effect on quality. Car and truck recalls exploded in the mid-1990s, hitting 20 million in 1999 alone.
Similarly, increased production, workforce reduction, and an overtime explosion are almost certain to increase the number of accidents and stress-related diseases. The Insurance Information Institute, an industry body, said as much in a July report on workers compensation: "Claim volume goes up when employment levels rise and the average number of hours on the job increases"
The escalation of detected OSHA violations toward the end of the decade points to an accumulation of negligence on the part of the major auto companies. How then is it possible that the injuries and illnesses declined?
CLANDESTINE CASUALTIES
The simplest answer is: underreporting.
As reported in Labor Notes last month, government figures on injuries and illness are based on unverified employer records and state workers compensation data which are also dependent on company honesty and accuracy. Changes in the state workers' compensation laws and insurance company policies in the last several years encourage companies to underreport in order to get lower insurance rates. OSHA audits have shown company reports to be 10-25 percent understated.
There are at least two ways a company can underreport. The first is to discourage workers from reporting injuries or illnesses, which is discussed below.
The second is to make extensive use of restricted duty. Technically, restricted duty cases are supposed to be reported to OSHA and the BLS. The fact is, however, they are easier to hide than cases that involve actual time off work. Unless they involve medical expenses other than those covered by health insurance, they will not appear on workers compensation records. These are the clandestine casualties.
An indication that both approaches to underreporting are used in the auto industry is that the overall injury and illness rate in assembly plants has fallen much faster from 1994 to 1998 than the rate for the more serious lost workday cases. In stamping plants, the rate of lost workday cases actually rose, while total (reported) injuries and illnesses fell.
Restricted workday cases are part of the BLS lost workday total, even though they don't involve time off the job. The official figures show that restricted work cases rose in all sectors of the auto industry in this period. Conversely, cases involving actual time off the job declined in every part of the industry from 1994 through 1998. What this points to is that, by one means or another, the companies are moving some of the most serious cases from time off work to restricted duty, while moving others to unreported restricted duty.
INCENTIVE
There is a strong economic incentive to do this. First, the costs of workers compensation did soar from the mid-1980s to the early 1990s. Companies that reduced the number claims were rewarded with lower rates. In fact, according to a BLS study, the number of such claims did drop after 1992. Ironically, however, this had the effect of raising the average cost of the remaining, presumably more serious, lost workday claims as much as 50 percent since 1995, thus pushing premium rates up. This, in turn, provided an incentive to reduce the number of cases that involve days off and are eligible for lost wage benefits. More of these were put on restricted duty where they could not claim the benefits.
This scenario also accords with the growth of programs to get workers who have had lost day injuries or illnesses back to work sooner under restricted work terms. In addition, several states have initiated workers comp "reforms" designed to get workers back on the job faster.
The official figures reflect all of this. What they don't show, of course, are the number of injured and ill workers placed directly on restricted duty, but not reported as such.
This is hard to prove, but the case of a Wisconsin plant owned by a major parts suppler points in this direction. Early this year, 150 out of 800 workers at this plant were on restricted duty, according to confidential company records. This would be a rate of 18.8 per 100 workers. In 1998 the average for the parts industry was 3.8 per 100. The wide disparity strongly suggests underreporting across the industry, while at the same time keeping as many people working as possible.
ZERO CONCERN
Despite proclamations about safety being a major concern, the health and safety philosophy practiced in the auto industry follows the "behavior-based" approach of the insurance companies. In this view, most accidents are the worker's fault. The United Auto Workers Health and Safety Department has condemned this approach as "generating fear and driving problems underground." It fosters underreporting by the workers themselves.
The companies employ a variety of such programs under different names: Delphi "4 Whys"; DaimlerChrysler "Zero Tolerance"; Ford-Visteon "The Danger Zone"; Ford "Health & Safety Leadership Initiative." Even where there is no official name, the attitude prevails that worker carelessness causes most accidents.
In many cases, workers are disciplined for reported injuries or illnesses.
In all cases, there is an arrogant callousness.
Nowhere was this more dramatically illustrated than in the death of a worker at DaimlerChrysler's Toledo, Ohio Jeep plant in May. It was completely clear in this case that the accident was triggered by continued production in the area adjacent to where the victim was making repairs.
Yet, in response to this fatal accident, as Labor Notes reported, a joint company/union policy statement distributed in the plant declared: "We endorse a policy of zero tolerance for injuries and for unsafe acts and/or conditions." Furthermore, it said, "employees who do not correct their unsafe behavior and/or who accept unsafe acts will be subject to discipline and/or removal from their positions."
A similar statement was passed out in all DaimlerChrysler plants, endorsed by the UAW International Union and the company.
Discipline for "unsafe behavior" was also reported by a worker at Ford's Buffalo, New York stamping plant.
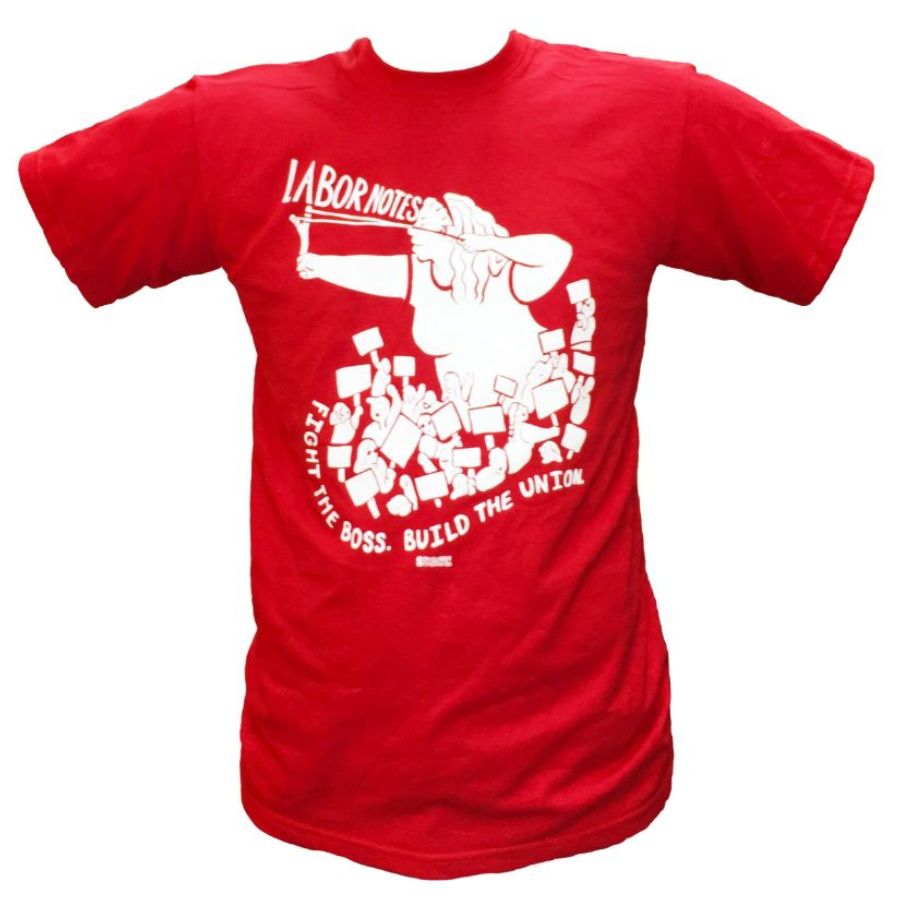
SUPPORT LABOR NOTES
BECOME A MONTHLY DONOR
Give $10 a month or more and get our "Fight the Boss, Build the Union" T-shirt.
Policies that link accidents to behavior rather than dangerous conditions and threaten discipline for "unsafe acts" discourage the reporting of incidents. Clearly, the companies know this.
The hypocrisy that underlies this approach can be seen in the explosion that killed six at Ford's Rouge complex in February 1999. The UAW reports that the flame supervision system that might have prevented the explosion had been disabled by the company in 1966. Since the late 1980s, four consultants and eight insurance company reports had recommended fixing the system. The company ignored all these warnings. Ford also withheld these reports from union health and safety representatives.
This UAW's summary, in fact, concludes that "union health and safety representatives are often not notified of and do not routinely receive copies of reports of inspections and audits beyond the scope of OSHA compliance. These include engineering evaluations of equipment, or evaluations of facilities by property insurance carriers. Audits by such outside experts often reveal serious deficiencies that have been overlooked for years."
At the level of management, there is no zero-injury mindset or zero tolerance for disaster--only an obsession to maximize production and profits. One worker put this disparity between policy and reality well. "Rules are black ink on paper, accidents are red blood on the floor," he said.
BLEEDING FOR DOLLARS
Besides dismissing workers for getting hurt or sick too often, the auto companies have other ways of discouraging workers from reporting incidents. In recent years, more and more plants have introduced absentee policies in which workers who accumulate too many absences can be dismissed regardless of the reason.
In some cases, management is not above bribing the workers to keep reported injuries or illness down. One of the more sinister examples of this is the "Safety Bucks" program at GM's truck plant in Pontiac, Michigan. Workers there call it "bleeding for dollars."
Under this program, workers accrue "safety bucks" when their unit has no recorded injuries. The bucks are used to order items, ranging from a Swiss Army knife to a fiberglass fishing boat.
The purpose of the plan, says one worker, is "to keep their recordable injury/illness numbers down." The driving force of the program is peer pressure. "The fear of disappointing your fellow workers by reporting a cut thumb or smashed finger," he says, "keeps most on the line from going to medical when they should."
A measure of how successful company strategies for discouraging accident and illness reporting has been comes from the National Council on Compensation Insurance. From 1990 through 1998, the Council reports, the frequency of workers compensation claims "per insured employee has dropped an amazing 24 percent."
UNION COMPLICITY?
Most of the examples given above involve facilities organized by the UAW. The union has a well-respected health and safety department and has recently won improved ergonomics language at some companies. Why then is there the sense that things have gotten worse?
Clearly, it is the companies who are the main culprit. But judging from the comments of rank and file members over the last few months, enforcement of contractual protections, OSHA regulations, and other laws affecting health and safety frequently gets lost in what might be called union politics.
One aspect of this is the atmosphere of "jointness" that the UAW has worked so hard to promote for the last decade. This view of unionism tells shop floor officials not to upset the company unless absolutely necessary.
While most of those responding to Labor Notes questionnaires said that union officials didn't discourage reporting health or safety problems, some indicated problems of enforcement. One Ford worker reported that his union rep said, "It looks bad [to report safety problems]," and that safety grievances are "just harassing the company."
A more common response was that officials don't follow up on problems. A General Motors worker reported that union officials "don't follow through on complaints." A Ford worker said that while officials don't discourage reporting problems, "they do little to deal with them." Another GM worker reported they don't "respond" to complaints.
One worker gave his officials a break, saying, "They are overworked."
In other words, the zeal of the union in enforcing health and safety contract terms and federal and state laws often does not match the persistence of the company in undermining them and discouraging the reporting of incidents.
WORKER-BASED SOLUTIONS
There is an alternative. The first step toward dealing with the real problems has long been known to health and safety advocates: Go to the workers. As the National Institute on Occupational Safety and Health suggests, "the person doing the job often has the best knowledge of the problem elements and insights into ways to improve work."
The British publication Hazards argues that such an approach can improve both the statistics that various agencies draw on and, assuming you have some power, help fix the real problem. Hazards proposes starting with an active program of worker-based research in which employees help shape the questions, participate in the research process, make the results available to all workers, and take "account of workers' experiences and subjective symptoms."
This completely sensible approach would, of course, lay bare the whole system of fraud covering up the consequences of the industry's relentless push for production. The companies will certainly oppose such an approach. It will probably be strongly resisted by union officials who give priority to the company's competitive agenda through "jointness" schemes. In other words, making such an approach a common practice will take a fight. But there are certain to be many local union and workplace leaders who want to take this kind of step.
A good place to start might be just to set an example and do something yourself, preferably with a group of like-minded workers. As Hazards suggests, "Do-it-yourself research can vary from a quick show of hands to a full worker-controlled scientific study." Start talking to people at work. Pass around a short questionnaire. Are there more or fewer accidents these days? Are people afraid to report them? Is the proportion of employees on "restricted duty" going up?
The political risks involved can hardly be greater than the existing risks to life and limb.
MORE INJURIES, NOT LESS
Twenty-three UAW members in 16 different auto facilities and one agricultural implement plant responded to a questionnaire sent out by Labor Notes. They reported 12 fatalities in 5 plants in the last two years. Six of these were the deaths at the Rouge plant in February 1999. When checked against OSHA records, one plant for which a respondent reported "no" deaths, showed one fatality.
To the question of whether there were more or fewer injuries in their plant, 16 answered "more," 4 the "same," and 3 "fewer."
In response to whether "the company puts production before safety," 13 answered "yes," 6 answered "sometimes," 1 "not always," 2 said "no," and 1 did not answer.
The question concerning a "behavior-based" approach to safety that blames the workers for injuries revealed that the safety training or policy in 13 of 17 facilities reflected this philosophy.
While this was not a scientific survey and the number of participants was small, it is clear that most who responded did not see any decline in injuries or illness in their plant or any rising concern for worker safety on the company's part.
JOINTNESS KILLS TRUTH AND WORKERS
By all accounts cancer from exposure to toxic chemicals and machining fluids is a greater danger in most auto plants than all the injuries and illnesses combined. These are not included in the Bureau of Labor Statistics' figures.
About ten years ago rank and file UAW members at GM's Lordstown plant formed an organization called Workers Against Toxic Chemical Hazards (WATCH). By looking a death records they established that cancer deaths at the plants were way above rates for the community. WATCH presented its results in 1989. Nothing was done in the plant, but the UAW initiated a joint company-union study.
The study established the link between the fluids and cancer, but the joint Occupational Health Advisory Committee named by GM and the UAW to oversee the study got the union to modify the wording of the study to lessen its impact. For example, where the first draft said there was "clear" evidence of a link between the cutting fluids and cancer, a subsequent draft stated that there was only "some" evidence.
As a result of the work of WATCH, the 1993 UAW-GM contract settlement reduced the exposure level of the deadly fluid significantly. Cancer-causing substances, however, have been found in many other situations and facilities in the auto industry.